A high-pressure reactor (magnetic high-pressure reactor) represents a significant innovation in applying magnetic drive technology to reaction equipment. It fundamentally resolves the shaft sealing leakage issues associated with traditional packing seals and mechanical seals, ensuring zero leakage and contamination. This makes it the ideal device for conducting chemical reactions under high-temperature and high-pressure conditions, particularly for flammable, explosive, and toxic substances, where its advantages become even more evident.
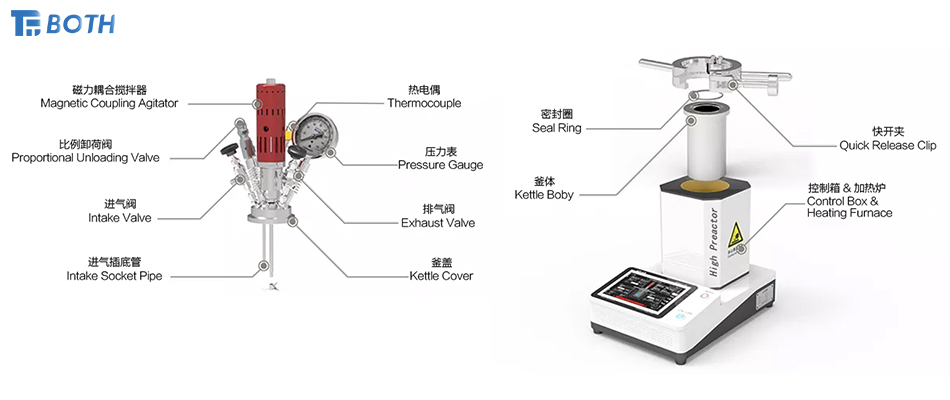
Ⅰ.Features and Applications
Through structural design and parameter configuration, the reactor can achieve heating, evaporation, cooling, and low-speed mixing required by specific processes. Depending on the pressure demands during the reaction, the design requirements of the pressure vessel vary. Production must strictly adhere to relevant standards, including processing, testing, and trial operations.
High-pressure reactors are widely used in industries such as petroleum, chemicals, rubber, pesticides, dyes, pharmaceuticals, and food. They serve as pressure vessels for processes like vulcanization, nitration, hydrogenation, alkylation, polymerization, and condensation.
Ⅱ.Operation Types
High-pressure reactors can be classified into batch and continuous operations. They are commonly equipped with jacketed heat exchangers but can also include internal coil heat exchangers or basket-type heat exchangers. External circulation heat exchangers or reflux condensation heat exchangers are also options. Mixing can be achieved through mechanical agitators or by bubbling air or inert gases. These reactors support liquid-phase homogeneous reactions, gas-liquid reactions, liquid-solid reactions, and gas-solid-liquid three-phase reactions.
Controlling the reaction temperature is critical to avoid accidents, especially in reactions with significant heat effects. Batch operations are relatively straightforward, whereas continuous operations demand higher precision and control.
Ⅲ.Structural Composition
High-pressure reactors generally consist of a body, a cover, a transmission device, an agitator, and a sealing device.
Reactor Body and Cover:
The shell is made of a cylindrical body, an upper cover, and a lower cover. The upper cover can be welded directly to the body or connected via flanges for easier disassembly. The cover features manholes, handholes, and various process nozzles.
Agitation System:
Inside the reactor, an agitator facilitates mixing to enhance reaction speed, improve mass transfer, and optimize heat transfer. The agitator is connected to the transmission device via a coupling.
Sealing System:
The sealing system in the reactor employs dynamic sealing mechanisms, primarily including packing seals and mechanical seals, to ensure reliability.
Ⅳ.Materials and Additional Information
Common materials used for high-pressure reactors include carbon-manganese steel, stainless steel, zirconium, and nickel-based alloys (e.g., Hastelloy, Monel, Inconel), as well as composite materials. The selection depends on the specific application requirements.
For more details about laboratory-scale micro-reactors and High Pressure Reactors, feel free to Contact us.
Post time: Jan-08-2025