Today, we see many freeze-dried foods in stores, such as freeze-dried fruits and fruit teas. These products utilize freeze-drying technology to preserve and dry materials. Before production, corresponding research is typically conducted in laboratories. As a professional manufacturer of freeze-dryers, BOTH has developed various models that are widely applied in many research fields. Understanding the drying process, especially the critical phase of secondary drying, is essential to the operation of freeze dryer.
In the freeze-drying process, secondary drying follows the sublimation drying stage. After the initial sublimation, most ice crystals have been removed, but some moisture remains in the form of capillary water or bound water within the material. The goal of secondary drying is to further reduce the residual moisture content to achieve the desired dryness.
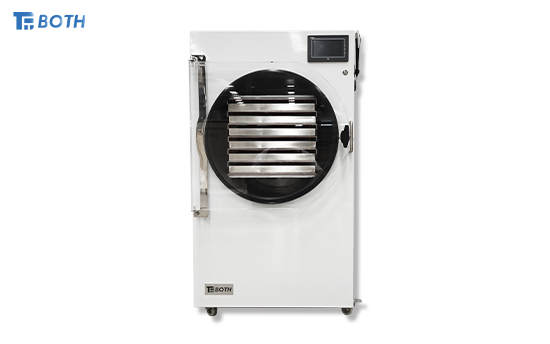
The secondary drying process primarily involves raising the temperature of the material. During this stage, the freeze-dryer gradually increases the shelf temperature, allowing the bound water or other forms of residual moisture to gain enough energy to detach from the surface or internal structure of the material, turning into vapor that is then removed by the vacuum pump. This process occurs at low pressure and typically lasts until the material reaches the specified dryness.
To ensure effective secondary drying, operators should pay attention to the following points:
Temperature Control: Set and control the shelf temperature increase rate appropriately to avoid rapid heating that could degrade the material or damage its structure.
Vacuum Adjustment: Maintain appropriate vacuum levels to ensure that vapor is quickly removed, preventing it from re-condensing on the material.
Monitoring Material Status: Use online detection methods (such as resistivity monitoring or infrared imaging) to monitor changes in the material in real-time and adjust process parameters accordingly.
Completion Assessment: Use preset endpoint indicators (such as material resistivity or weight changes) to accurately determine whether drying is complete.
Secondary drying is a crucial part of the freeze-drying process. By finely controlling this stage, the final product quality can be enhanced. With the help of professional equipment manufacturers like BOTH, enterprises and researchers can not only meet complex production requirements but also maximize economic benefits while ensuring product quality.
When considering purchasing a freeze-dryer, BOTH products are a worthy choice. They excel not only in hardware but also in software control systems. BOTH freeze-dryer series employs advanced PLC control systems, complemented by user-friendly interfaces, making the entire freeze-drying process more intelligent and automated. Additionally, BOTH places a strong emphasis on environmental protection, significantly reducing operating costs while providing cost-effective options that meet users' diverse needs.
If you are interested in our freeze dryer machine or have any questions, please feel free to contact us. As a professional manufacturer of freeze dryer machine, we offer a variety of specifications, including household, laboratory, pilot, and production models. Whether you need equipment for home use or larger-scale industrial equipment, we can provide you with the highest quality products and services.
Post time: Oct-28-2024