Multiple Stages Short Path Wiped Film Molecular Distillation Machine
Traditional Distillation | Short Path Molecular Distillation |
Boiling point differences | The mean free path difference of molecular motion |
Ordinary Pressure or Vacuum | High Vacuum (usually 10~0.1Pa) |
Higher than boiling point | Lower than boiling point (around 50~100℃) |
Long | Short (usually several seconds) |
Low | High |
Normal material | Thermosensitive material |
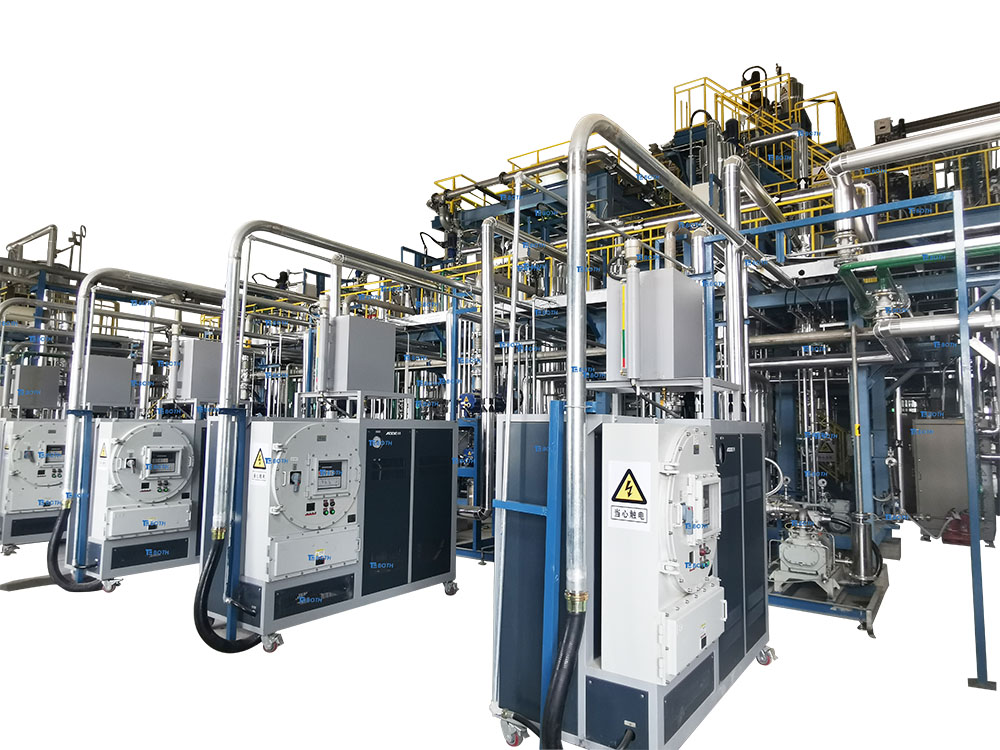
● Operating temperature is low (lower than boiling point), with high vacuum (no load ≤1Pa), heating time is short (several seconds) thus no thermal decomposition occurs and the efficiency of separation is high. Specially, it is adapted to separation of high boiling point, thermosensitive and easy oxidized matters.
● Removing low molecule material (odor removal), heavy molecule material (decolor) and impurities of mixture.
● The course of molecular distillation is a physical separation, preventing separated products from pollution, especially keeping original quality of natural extraction.
● Oil diffusion pump with unique nozzles has a very high compression ratio, and the back pressure can reach more than 160 Pa, the energy efficiency ratio is improved.
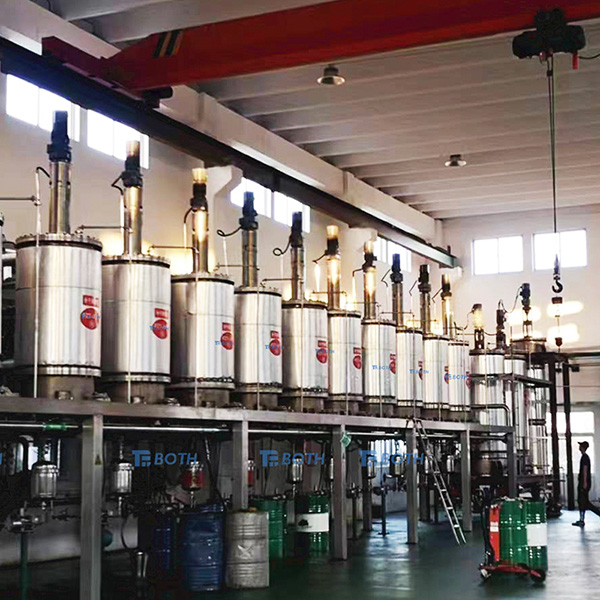
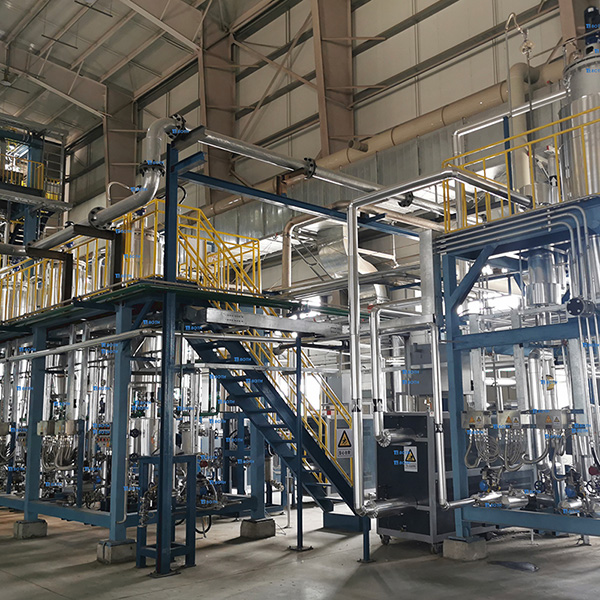
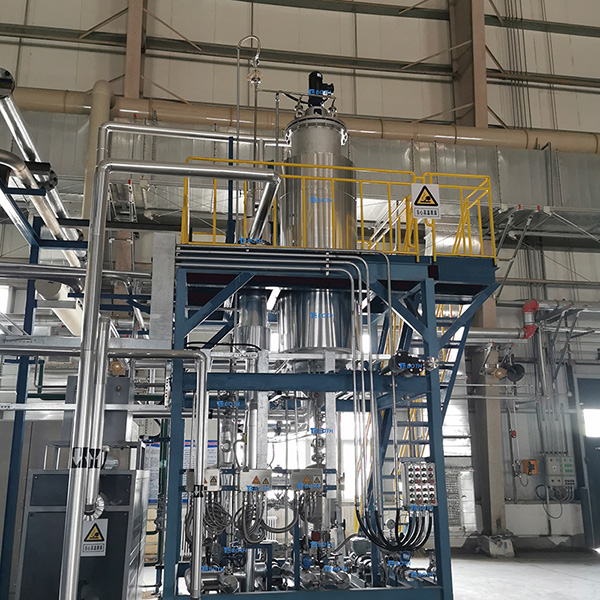
Application | Typical Material |
Daily-use Chemical Industry and Cosmetics | Various oils and essential oils, rosemary essential oil, lanolin, lanonol, natural plant extracts, protein hydrolysate, antiseptic substance, etc. |
Pharmaceutical | Amino acid esters, glucose derivatives, solanesol, perilla alcohol/ DIHYDRO CUMINYL ALCOHOL, lycopene, garlic oil/ nervonic acid/ selacholeic acid, terpenoid, Herbal oil, synthesis and natural vitamins (vitamin A, vitamin E,tocopherol , β carotene), palm oil/ carotenoid / carotinoid, etc. |
Additives | Fatty acids/FFA and their derivatives, fish oil refining/Ω-3/DHA+EPA, squalene, rice bran oil, perilla seed oil/α-linolenic acid, coconut oil/C8 oil/MCT oil, various flavors, spices, etc. |
Plastic Additive | Epoxy resin, phenolic resin, isocyanate, plasticizer, acrylate, polyether, olefin oxide, etc. |
Pesticide and Surface Active Agent | Permethrin, piperonyl butoxide, omethoate, alkyl polyglycoside/APG, erucyl amide, oleamide, etc. |
Mineral Oil | Synthetic lubricating oil and lubricants, paroline, tar, asphalt/pitch, waste oil recovery, etc. |
Remark: Products with Bold font is the high-value-added product.
1) What determines the process capacity of a molecular distillation machine?
The main determinant is the evaporation area, which is called as efficient evaporation area/EEA. Usually, we are able to produce from 0.1M²~30 M².
Then, the vacuum condition and the characteristics of the feeding material also effect the process capacity. So, should we ignore the difference feeding material to define a certain process capacity, it is not practical.
In theory, the processing capacity is as follows: feeding rate per square meter per hour is 50-60KG (take the equipment over 2 square meters as an example, and according to different material characteristics)
2) Why we need a multiple stages molecular distillation machine, what’s the difference from a single stage one?
According to actual needs, the machine can vary from one stage to multiple stages’ (each stage is an evaporator and related supporting facilities). The stages are connected in series, and the work tasks of each stage are different. Such as deodorization, extraction of different components, or gradually increase the product purity.
Besides that, the multiple stages molecular distillation machine can reach a balance of the vacuum condition. It can reach a high product purity just with one pass. While, a single stage would need several pass and should be clean after each pass. That is why the single stage machine is usually adopted in R&D or pilot scale production, while, a multiple stages molecular distillation machine is used in commercial production.
3) As an ender user, how to choose a multiple stages molecular distillation machine?
The processing capacity determines the evaporation area. The product characteristics determines the manufacture material (whether there is any corrosion, etc.). The separation content and the requirement to be achieved determine the stages and configuration (such as scraper design, vacuum configuration, cold trap, refrigeration power, heating power, etc.).
So, a multiple stages molecular distillation machine is a custom product. As a manufacturer must have a good understanding of the material before designing and producing it.
Fortunately, we have a great technical support team and experienced engineers who can help you understand your product and your demand. For special materials, we also provide a short path distillation trial service.
4) Is it a turnkey machine?
Yes! It is a turnkey machine come with all the supporting facilities such as heater, chiller and vacuum